Back pressure is an important parameter used in the injection molding process. It helps control the quality of the molten material and the resulting products.
Specifically, it can be used to reduce air on the product’s surface, glue walking around the product, and shrinkage. To achieve this, the back pressure must be at a minimum level.
What is back pressure?
Back pressure is an important parameter to control the quality of molten plastic material and products in the process of injection molding.
The back pressure of the injection molding machine is a critical parameter to control the quality of products and molten materials.
When the back pressure is too high, the screw may retreat and the molten material will be less dense at the front end of the screw, causing more air to enter.
This can lead to poor plasticization and instability of the injection molding process. It can also cause significant changes in the weight, size, and surface of products. All of these factors can affect the overall quality of a product.
Back pressure is often ignored in the process of injection molding. However, it is an important parameter that is important for controlling the quality of the molten material and products in the process. Several other parameters must be considered, but back pressure is an essential one.
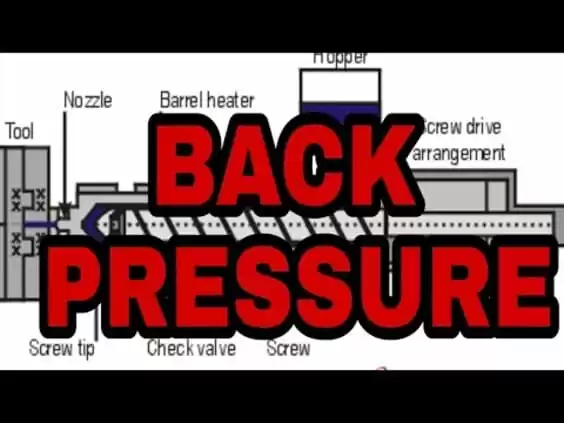
Back pressure is a parameter that must be calculated before the injection process. The opening pressure must be high enough to hold the mold open and maintain the injection speed.
However, once the mold is filled, high injection molding pressure is no longer necessary. It can reduce air on the surface of the product.
Back pressure is a process parameter that affects the quality of the molten material and the final product. It reduces air on the surface of the product and is a key control parameter in injection molding.
High back pressure increases the consistency of the molten plastic and improves the gloss of the finished product. Injection molding should be performed with a back pressure of three to fifteen kilograms per cubic centimeter.
Back pressure in injection molding can be achieved by controlling the temperature of the product. When the melt temperature control of the mold is higher than the ambient temperature, the molten resin will flow more smoothly.
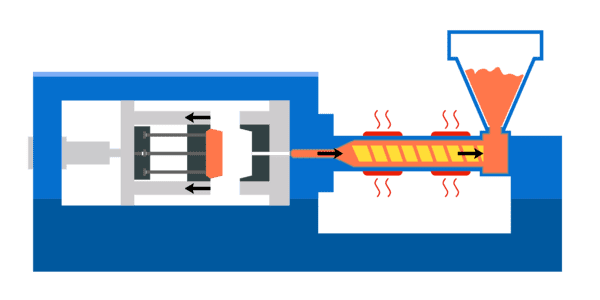
If the temperature is lower than the ambient temperature, the material will be too cold before the injection process is completed. The melted plastic will not flow through the mold if trapped air is trapped on the surface.
To overcome this problem, the injection speed and pressure can be adjusted. Increasing the mold temperature will also help to prevent premature cooling of the material.
Back pressure is primarily of concern in the injection area, but can also occur in the clamp pressure unit of the
injection molding machine.
A good way to reduce the air on the surface of the product is to use a large gas vent and mold vacuuming.
Proper gas venting will eliminate any air trapped on the surface of the product and prevent substandard welds. It can reduce the shrinkage of the product surface.
How backpressure affects injection molding?
Injection molding requires good control of back pressure. This helps reduce the amount of shrinkage of the product’s surface and improves product quality.
To ensure quality, work with a plastic injection molding company. This ensures you get the highest quality product possible. Back pressure is not an option on every machine.
When using high back pressure, it is essential to check the length of the fibers. This is important because long fibers are more likely to break.
When choosing plastics for injection molding, always keep in mind the manufacturer’s recommendation and the maximum pressure the plastic can withstand.
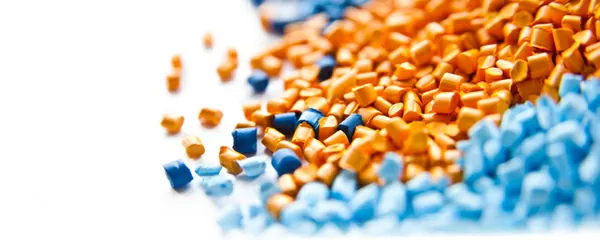
Back pressure in injection molding can be adjusted according to the product’s structure, size, and color. It is generally set between three and fifteen kilograms per cubic centimeter.
When using high back pressure, be aware that it will cause excessive holding pressure on the injection molding machine. It can also result in defects along the parting line or boundary.
Unlike high-pressure molding, back pressure does not raise the melt temperature, but it will increase the speed of the injection screw.
The screw is responsible for 70-90% of the energy needed to melt plastic, so it is essential to adjust back pressure accordingly. It can reduce glue walking around the product.
Back pressure in injection molding is a factor that can help minimize glue walking around the product. This pressure is usually set at three to 15 kilograms per cubic centimeter.
The exact back pressure needed for a specific product depends on its structural design, the quality of the raw materials, and drying conditions.
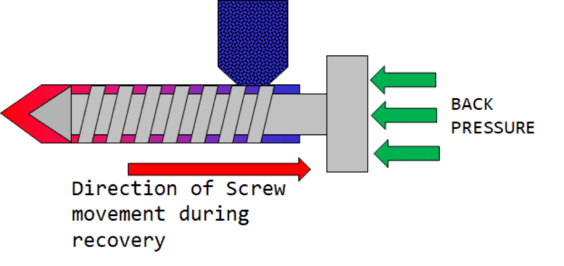
Back pressure exerted in injection molding can also increase during color mixing, airiness, or shrinkage. It can also be decreased to reduce the effect of salivation or glue leakage.
Proper back pressure in injection molding is critical to achieving the best plasticization quality. Without it, the injection unit volume is unstable, and glue walks around the product. Low back pressure can also lead to product weight and size changes.
It can also cause the glue to leak out of the nozzle and reduce plasticization efficiency. Moreover, excessive back pressure can lead to the premature burnout of the heating ring near the nozzle, and increase the mechanical wear of the pre-molding mechanism.
Proper back pressure in injection molding is also important for the quality of the molten material. It can help eliminate the possibility of glue walking around the product.
Proper back pressure reduces the amount of glue walking around the product and keeps the screw in the bottom of the products. Proper back pressure also helps in the removal of old colorants during color change.