During the practical application of plastics production, there are special plastic products with shape structures, and the primary injection molding is often difficult. Work with a kind of high-efficiency plastic product connection method, ultrasonic energy wave welding technology to shorten product production time and high production efficiency.
However, due to the peculiarity of ultrasound wave welding, this welding method is used by non-proprietary plastic cities. What kind of plastic modification is suitable for ultrasonic waves? The principle of working with supersonic wave connection needs to be understood first.
Ultrasonic welding uses high-frequency vibration waves to contact two object surfaces, and under pressure conditions, the two object surfaces are mutually frictionally formed to form molecular layers.
The main electrical components of the ultrasound wave connection system include a comprehensive ultrasound generator, a processing device, a variable-width rod, a three-piece unit, and a machine rack.
Ultrasonic welding principle
1) Ultrasonic plastic welding principle: When ultrasonic waves act on the thermoplastic plastic contact surface, high-frequency vibration occurs every second of production, reaching a constant amplitude and high-frequency vibration. Due to the high temperature of the local area produced by the joint, the noise at the two joints is large.
In addition, due to the difference in the thermal properties of the plastic, it can not be delayed for a while, the fire zone is concentrated, and the two plastic contact surfaces can be quickly melted.
After the ultrasonic wave is stopped, the pressure is kept on for a few seconds, and the solidification is formed, so that a solid molecular bond is formed, which reaches the ultrasonic welding techniques purpose, and the strength of the welding cycle is close to the strength of the raw material.
Ultrasonic plastic welding technique has a good selection of three factors, including the amplitude of the flexible device, the applied pressure, and the welding time.
The interaction of these three quantities is appropriate when the capacity is exceeded, the amount of plastic melting is large, and the material is easy to deform; This maximum pressure is the maximum pressure of 1mm for the maximum length of contact.
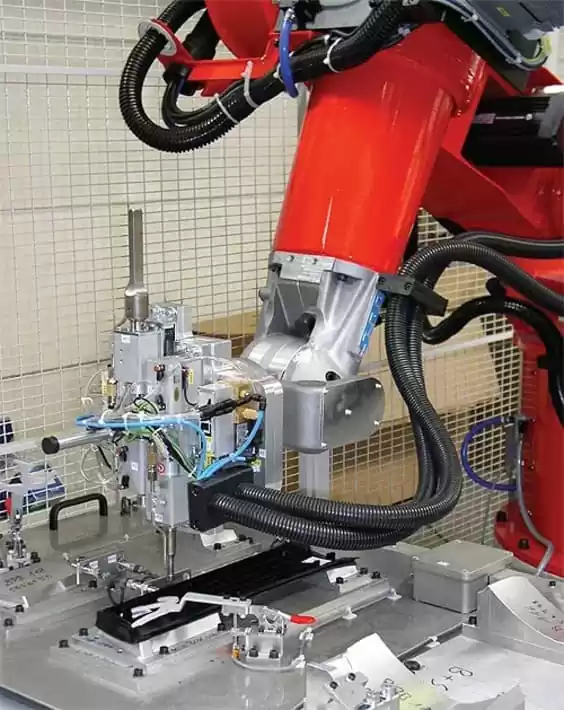
2) Ultrasonic metal welding principle: Ultrasonic metal welding principle uses ultrasonic frequency (exceeding 16KHz) mechanical vibrations capacity, a special method for connecting homogeneous metals or dissimilar metals.
When the ultrasonic wave is connected to the metal, there is a high-temperature heat source in the non-conforming construction work, and there is only a static pressure, and the vibration capacity of the stile will change due to the friction effect between the construction, the shape change, and the finite temperature increase.
Indirect metallurgical bonding is a kind of actual bonding under the conditions of non-fading melting of the base material. Due to this, the effect has been overcome. Ultra-sound metal joints can be used for single-point welding, multi-point welding, and short-strip welding for colored metals such as copper, silver, copper, and steel. Can be used for holding silicon wire, breaker piece, electric wire, battery electrode, and ear plug.
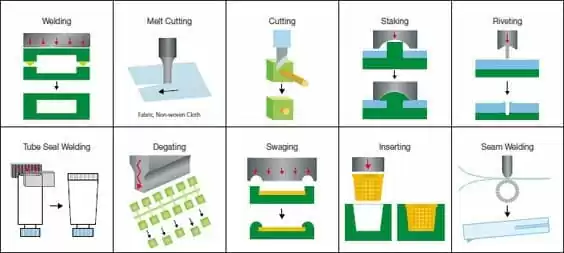
Ultrasonic wave welding
1) Welding method: Ultrasonic ultra-high frequency vibration under pressure, frictional heat, and instant fusion bonding to create a plastic joint surface between two blocks, strong welding strength and beauty, suitable work, and rational joint designed to be watertight and airtight, with no inherent inconvenience, high-efficiency, and clean welding.
2) Molding: This method is similar to the flame method, and the concave flame head is pressed onto the outer surface of the plastic product. Appearance is smooth and beautiful, this method is widely used in electronic devices, fixed molding of lenses, and fixed lenses of chemical products, etc.
3) Implantation: Borrowed flame head and appropriate pressure, momentary metal zero (such as screw mother, screw rod, etc.) inserted into the mold hole, fixed at a certain depth, after completion, no learning force, force equality beauty The strength of the molding inside the traditional model, the injection mold acceptance exemption and the injection failure.
4) Iron flame: The iron flame method is vibrational flame compression control, and the protrusion of the article is used to heat the iron, and then the two objects are mechanically welded.
5) Pointing point: Pointing point is because the point is not easy to design because the point is pointing point point point, the same welding effect can be reached.
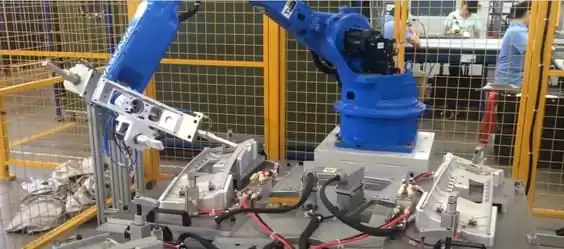
Ultrasonic welding material
The combination of technology and materials is a perfect combination of talent and benefits. Do you use ultrasound welding technology for suitable materials?
1. Ultrasonic welding is not suitable for all types of plastics, and the plastic melting point is relatively low when using materials that require ultrasonic welding technology.
The product’s flame line design takes into consideration the characteristics of the product itself when used. Amorphous plastics such as ABS, PMMA, PC, PS.
2. Material use of plastic body attributes is an important factor in consideration of demand, such as a fixed shape or a crystalline body. The effect of connecting plastics that are not compatible with each other will hurt the quality of the results.
3. Suitable non-woven fabrics for ultrasonic weldings, such as thermoplastic fabrics, composite materials, copper plates, and mixed fabrics.
4. Flexible material: finger-quality, low-tensile weight material.
5. Flexible dissimilar materials: materials with high tensile strength and low mechanical vibration resistance factors, such as polystyrene (PS), and polyphenolic acid (PMMA).
6. Proprietary polymer thin film, molecular synthetic fiber, thin film Japanese fiber compositional fabric.
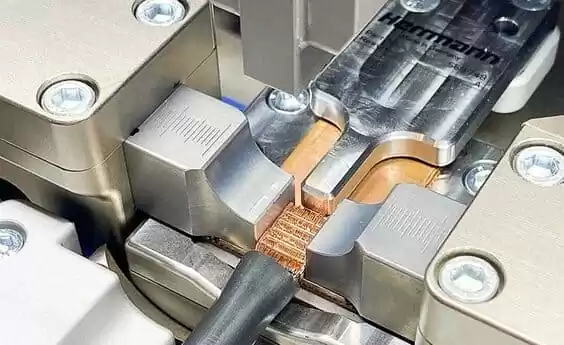
Ultrasonic welding port design
Ultrasonic welding requires a small welding port and a single contact surface. Factors such as fitting design decisions based on welding materials, mechanical shapes, and mechanical requirements.
Usually contiguous triangular part convergence super vocal capacity, rapid fusion formation contact surface. The left and right divisions are connected, the stairs type and the tank type.
When the cutting mold is applied to the demand seal or the plastic is in a narrow temperature range, the melting state is rapidly changed from solid to solid.
Features of ultrasonic welding
Ultrasonic has a wide range of applications, energy saving, environmental protection, and high precision.
Advantages of ultrasonic metal welding:
1. The welding material does not melt and does not have fragile metal properties.
2. Good conductivity after welding, and the resistivity is extremely low or almost zero.
3. Low requirements for welding metal surface, can be welded by oxidation or electroplating.
4. Short soldering time, no need for any flux, gas, or solder.
5. Welding without sparks, environmental protection, and safety.
Advantages of ultrasonic plastic welding:
1. Fast welding speed, high welding strength, and good sealing performance;
2. Replace the traditional welding/bonding process, low cost, clean, and pollution-free and will not damage the workpiece;
3. The welding process is stable, and all welding parameters can be tracked and monitored through the software system. Once a fault is found, it is easy to eliminate and maintain.
Disadvantages of ultrasonic welding:
1. When the thickness and hardness of the welding workpiece increase, the power required for welding increases exponentially, thus increasing the manufacturing cost of the ultrasonic welding machine.
When the required power is too large, the design, manufacture, and process effects of the acoustic system will produce a series of difficult problems to solve.Therefore, currently, it is mainly limited to the welding of thin and thin workpieces such as wire, foil, and sheet.
2. The joint form of the current ultrasonic welding system is limited to lap joints, and due to the limitation of the tool head, the workpiece can only be extended within the allowable size range of the welding system, and the welding joint form and size range is limited.
3. At present, it is difficult to detect the quality of ultrasonic welding. It is difficult for general detection methods to monitor in real-time during the production process, and the method of non-destructive testing has not yet reached a popular state.
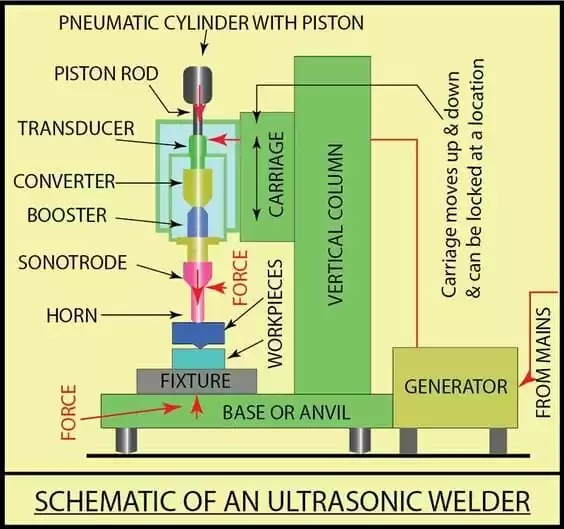
Application of Ultrasonic Welding
1) Automobile: Ultrasonic can be controlled by a computer program to weld large and irregular workpieces such as bumpers, front and rear doors, lamps, brake lights, etc.
2) Household appliances: Ultrasonic can be used for: portable fluorescent lampshades, steam ironing doors, TV casings, recorders, transparent panels of audio ultrasonic welding machines, power rectifiers, TV casing screw holders, washing machine dehydration tanks, etc. Need to be sealed, firm, and beautiful of home appliances.
3) Packaging: the sealing of the hose, and the connection of the special packing tape.
4) Toy industry: due to the use of ultrasonic technology to make products clean, efficient, and firm, the use of screws, adhesives, glues, or other auxiliary materials is eliminated, which reduces production costs and greatly enhances the competitiveness of enterprises in the market.
5) Electrical engineering: plugs, wire plugs, contact reeds, sockets, wire reels, spools, contacts, fluorescent tube boxes, electric fuses, relay switches, plug injection plastic parts, printed circuit boards, fuse boxes, etc.
6) Other commercial purposes: Ultrasonic welding equipment can be used for communication equipment, the computer industry, printing equipment audio-visual products, etc.